Project Gallery



This is some of the flat work machined in house, the one is .003" thick Capton material. The next one is bakelite and one is 2025 aluminum with .0005" true position locations.



This is a part for an aerospace application made out of hard brass. It is made out of a solid plate and is .006" +/-.001 thick with most of the other tolerances +/-.001". The customer had a stack of no-quotes 3" high. Diligence, Inc. tackled the job and made it affordable..
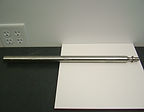
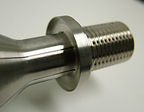
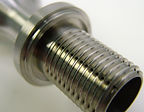

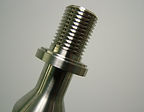
This is a part made for NASA. Made out of 316 SS with a 20.625" length and an O.D. of .937" +.001/-.000 , an I.D. of .860" +.001/-.000 which creates a .040" wall thickness. The tube has a straightness callout of .002". If that wasn't complex enough, it has 6 grooves around the outside that are .011" +.001/-.000 wide and .012" deep. These grooves go the length of the tube and follow the contour down and line up with (6) .016" dia. holes that are .937" deep. This job was lost to a lower bidder, but we got it back because they couldn't make the part. We are thank ful for the opportunity to do this project.

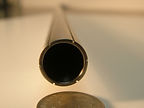


This part was the reason we got a shot at the other tube. This one also had the other close tolerances and the grooves, but didn't have the welded on nose.

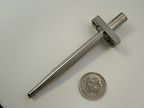
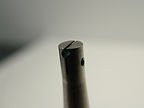

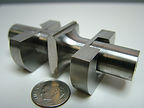
These are titanium transducers. The longer part has (2) .031" wide arcs that are right next to the .250" dia. shaft. the arcs were .090" deep and almost 2.5" away from the end of the part. The hole in the end was .0627" with a tolerance of +/-.0001. At the time we did it in house with our wire EDM.
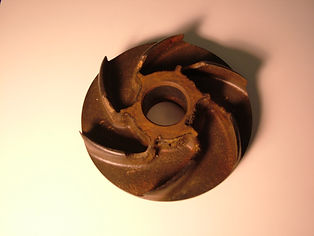
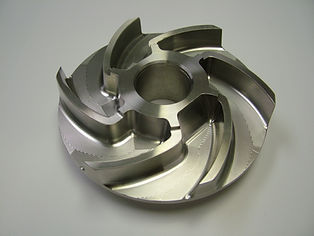
Original Impeller
Cast Iron
Re-designed Impeller
304 Stainless Steel

Re-designed grinder impeller made of S7 Tool Steel. Unit gave twice the life for the customer's operation.






Diligence machined these various parts for different customers. We can machine most materials, Plastics, aluminum, brass, tool steels, stainless steel and exotic alloys are some of the materials Diligence has machined.


Diligence created these parts for the plastic extrusion field. H13 was used for the acme threaded part. The inlet unit was 440 C Stainless Steel.

While consulting, these were some medical parts that were reprocessed for optimization. the top one is a titanium screw that was programmed to machine faster. the left round part was put in a smaller machine with more capability. A thread deburr sequence was also added to keep the part from operator intervention. The middle round part's time was shaved to a minute and a half. The far right round part was deburred in the machine to help reduce operator deburring.
the next screw was a bone screw that was made out of some kind of proprietary stainless steel...it was very difficult to machine. Constant surface feet per minute and different tooling reduced problems and cycle time. The bottom screw cycle time was cut in less than half with programming and tooling changes.
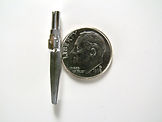
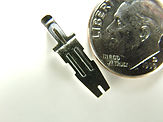



Diligence while consulting created these parts on a customer's machine. These parts are for the medical field. They have many details on them, and at the same time they were made out of 50 Rockwell 17-4 stainless steel. Now in production, they are heat treating afterwards. We engineered the program and even special tooling to do the complicated machining process. The customer wasn't even going to make the parts, but the process turned out very good, and now they are needing to get more machines for the amount of parts the customer wants!
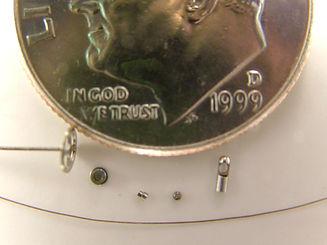

Diligence while consulting created these parts on a customer's machine. The smallest parts on the page were called the "Spec". The CAD picture next to this image is what the "Spec" looks like. Completely burr free and extremely miniature. The one part looks like a steering wheel for an ant's car. It was made of titanium. The part that has the shape of a bullet was modified to make it more burr free.




This is a fixture that Diligence designed and built. It has pull back spring locators. Once the part was located and clamped, the locators could be moved out of the way. This was accomplished by using the machine in cycle to trip the handles. Diligence also programmed and set up this fixture at the customers site.






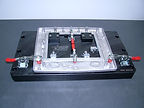

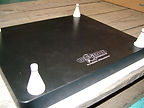
These are some of the other fixtures that were built for this customer. They are all hardcoated aluminum for durablility and many years of use. The Parts held are made out of magnesium and Diligence Programmed, ordered tools and set the jobs up. The customer was very happy with the results.




This is a Diligence designed and built optical gaging fixture for a Smart Scope vision system. It is held in a clamping fixture that locates the fixture on the top surface of the Smart Scope table. The fixture holds 25 parts vertically and 25 parts horizontally. All locators are self contained to keep out any contaminants. It is made out of 6061 aluminum and hardcoated for durability. It has finger pull back tabs for operator loading. Clearance is made all the way around the part for visual inspection.
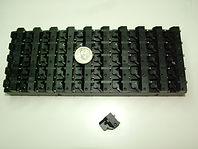

This is a Diligence designed and built optical gaging fixture for a Smart Scope vision system. It is held in a clamping fixture that locates the fixture on the top surface of the Smart Scope table. The fixture holds 50 parts vertically and 50 parts horizontally.

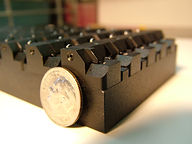
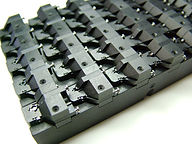
The customers parts were very tiny rings that needed to be measured vertically and horizontally within a few tenths. They also wanted the fixture to measure five different sizes. The smallest ring is .028" in diameter and the largest is .089" diameter. Wall thickness is .003".
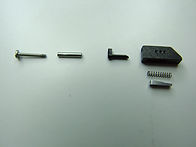

Diligence designed and built this fixture to satisfy the customers requirements. Each fixture block containes a vertcal and horizontal spring locator plus a 3 position main locator to cover all of the different size rings. All locators are self contained to keep out any contaminants. The plungers come in at 7 degrees to give downward pressure at the same time they locate the part. The stainless steel threaded screws are covered with a hypodermic tube to create a smooth feel. The fixture is made out of 6061 aluminum and hardcoated for durability. The horizontal parts locate on a hard acrylic transparent pad. This fixture contains over 1000 components.

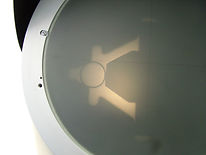
Here is the fixture in Diligence's optical comparator at 50X magnification. These two pictures show the minimum and maximum sizes this fixture locates. The locator is coming in from the right side. These are the horizontal oriented parts.

This is one side of a fixture system for the Dana Corporation that was designed by Diligence Inc. The setup simultaneously held 16 parts. A special locating pin was designed to make the fixture endure many cycles.

These parts were programmed and run on a Citizen B12 Swiss CNC - The result: cycle times made the owner's eyes open wide. Previously they had been having another company machine them, and now they are doing it in-house.

These parts were programmed on a Citizen L20 type 7 Swiss CNC. The one on the top left ran at 38 seconds..in 303 stainless steel, it was flying. We optimized it for a faster cycle time - always looking for efficiencies. The other two parts were programmed complete and setup for a customer when working at Productivity.
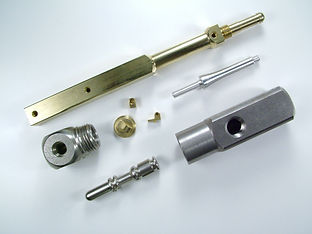
These customers parts were programmed and setup while working at Productivity, the brass part was being done in more than 2 OPS in a turning center and now - in the L20 type 5 Swiss - it is done in one operation at half the cycle time - the arrow tip ran 18 seconds in a Citizen B12.

The large part was programmed and run for video footage on a Citizen M32, the other parts were for shows - made on a B12 Citizen. The top parts are bullet sinkers for fishing that hold scent and the bottom part has a wall thickness of less that .001" - demonstrating the abilities of the Swiss style machine.

These automotive parts were optimized on Swiss CNC machines. The owner made the comment, "Bruce really knows how to get the time out of jobs that are running!

This small sword was made in a Citizen L16 Swiss machine out of round stock. Tiny? yes, but also very sharp!
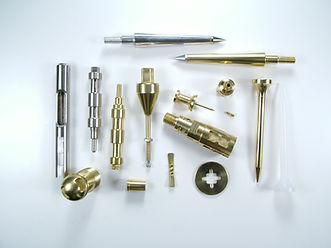
Here are more parts made in class, the one on the bottom left middle ran in 22 seconds with a parts-per-chuck program in a Citizen M20. The part in the middle of the bottom row that looks like a snow board IS a miniature snow board.

This was a class part that used pinch turning with the turret and the gang in the Citizen M20 Swiss CNC.


Class pen that was used for open house for Remmele Engineering.
Close up of pen parts to show off the required intricate machining cuts.

Finished product - the employees at Remmele Engineering Plant 30 each got one with their name engraved on it.

These parts are for tightening a snowmobile clutch. The brass part was the prototype. The class learned pinch turning and turning with the sub spindle clamped on. The machine used was a Citizen M20.

This is a dart that was made in a Citizen L16 and then later in a Citizen M20. It actually worked well as the class brought a dart board to test it.